Having the ability to check in on information remotely can be essential to businesses
Whether a company has locations that span the globe, or another location on the other side of town—having the ability to remotely monitor automated systems is extremely helpful and sometimes very essential. Here we will go over the two ways that having remote monitoring capabilities can benefit your business.
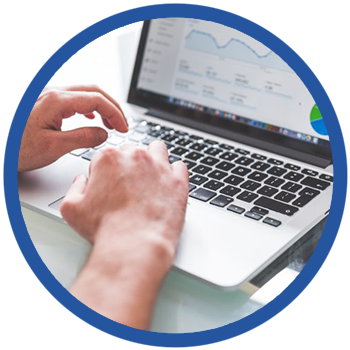
Remote Monitoring Systems (RMS) keep an eye on automated processes and provide information that can be accessed from anywhere off-site. Whether it’s across town, at the local coffee shop, or across an ocean; these systems can be specifically programmed to monitor and analyze a bunch of different factors and situations 24/7. With that being said, there are two main reasons for having a RMS. The first reason is to be able to monitor the systems to ensure they are operating as they should be. For example, a rare books collection in a library would need to ensure that the humidity and temperature in the rare books room is always set to an exact number. If the temperature or humidity were to go up or down just a little the books could be damaged or ruined. In this case, a RMS could keep track of all of this information and make sure that the proper temperature and humidity is kept. If something were to go wrong, the system would notify the person in charge of maintenance for the collection so they could resolve the issue and restore the conditions of the room back to normal.
This leaves us with the second main reason a RMS would be used: a RMS can perform a self-diagnosis and determine when a machine or system is not acting as it should. When an error occurs or a component unexpectedly shuts off, the contact person for that machine/process will receive an alert either by email, text, or phone telling them that the system is having an issue. The system itself also runs an internal analysis to diagnose the issue, so when the contact person receives their alert they know exactly what’s going on and from then on effort can be spent fixing the problem. Such a quick diagnosis also means that it takes much less time to resolve the issue. Instead of having a technician physically look at the component or system, which takes much more time, the system will diagnose the error itself. Taking the guesswork out of diagnosing the issue shortens the repair process, and also means that machines and systems have less downtime and spend more time running processes. In short, this means more productivity and more profit! Knowing all of this, companies can breathe easier knowing that their systems are monitored around the clock.
In addition to analyzing processes and diagnosing critical errors, remote monitoring systems also self-perform regular checks to make sure that processes are running correctly. These self-checks give companies peace of mind because if an error is made in a physical inspection—or a physical inspection is completely forgotten about their systems are still being maintained. The idea is to find potential problems and resolve them before they ever become issues. So if you work in-office and are responsible for a rare books collection or if you’re a remote manager of a high-volume assembly line working across the country, a remote monitoring system has your back and makes sure things run smoothly.
Let’s Get Connected