Situation

Glue Dots International (GDI), a revolutionary adhesive company owned by Ellsworth Adhesives Corporation, selected Automation Solutions as their automation partner upon recently acquiring another business and expressing the desire to expand into a new state of the art production facility. This presented an opportunity to merge and automate multiple systems – ensuring a more consistent outcome by accurately regulating variability and improving processes, while generating cost savings. The former antiquated process was predominantly manual and required a high degree of physical tasks and close monitoring.

We meet customer needs with both proven experience and innovative custom solutions.
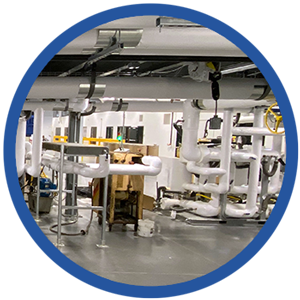
“Automation Solutions has been a solid partner for us. We originally started to work with them on small scale projects in our previous production facility. Their responsiveness and ability to deliver effective solutions gave us the confidence to use them for designing and implementing the process control in our new facility. Throughout the project they were able to come up with unique solutions to meet our needs as well as meet an aggressive timeline that we laid out for project completion.”
~ Eric Mealy, Engineering Manager
Glue Dots International
Opportunity
GDI sought a partner who could develop, orchestrate and implement an automation solution to be applied across a reimagined manufacturing process. The process needed to combine existing reliable machinery, recently acquired parts (highlighted by new motors and vats), and newly designed procedures and controls; all of which could be monitored both on-site and remote. At its core, the requirements of this project featured recipe batching conducted at a controlled temperature and pressure, while coordinating the flow of specific ingredients through regulated valves to create the optimal mix at the precise time. Another layer of complexity was the need to implement the solution simultaneous with the construction of the company’s new manufacturing facility.
This particular challenge was unique as both the client and solution provider needed to account for a high degree of uncertainty due to the project’s nature, the coordination of introducing new machinery to an existing process, and the consolidation of two separate business units into a new manufacturing facility. Automation Solutions history of success working in ambiguity, proved to be a perfect fit for GDI, as there were numerous occasions requiring the ability to adapt and provide solutions “on-the-fly” for unanticipated situations.
In March 2020, the world was struck by the COVID-19 pandemic interrupting many business’s ability to function. Automation Solutions, deemed an essential business, was able to remain nimble and flex (through an integrated effort of remote design, build, and coding, combined with approved on-site safe business practices) to coordinate the manufacturing, delivery and installation of parts and components to meet GDI’s objectives.
Implementation
An end-to-end automation solution was developed in partnership with the client (GDI), the new construction general contractor, the builder, and the electrician. Automation Solutions design complimented the client’s desire to create a modern, innovative manufacturing facility with custom programming and applied technology to help future-proof their production process while allowing for the ability to expand. The ability to deliver a turn-key solution across engineering, panel building and contracting simplified what could have been a cumbersome process. Having all phases of the process completed by a single controls house ensured complete accountability, streamlining the channels of communication between the client and the previously mentioned contributors to the project as a whole.
The heart of the solution featured the construction of two custom designed 2-door 72” x 72” cabinets housing the panels providing integrated plant-wide controls through a PLC programmed for compatibility with both the new parts and the reused reliable machinery. The system can be monitored onsite through a series of HMI touch screens providing the control and alerts of all functions including multiple fail-safes to limit the potential for mistakes. It is also available through a remote connection for troubleshooting by off-site technicians. Reporting data is continuously collected and can be accessed as required by management and individuals provided the appropriate permission levels. This custom solution, allowing both on-site and remote monitoring with options for 24/7 support, highlights Automation Solution’s ability to deliver throughout the entire process of engineering, design, building and installation.
“This project was a great testament to not only the firm’s capabilities; but it really showcased how we like to work. We were able to operate as one team throughout the partnership, sharing the same vision and goals. It was truly a collaborative effort allowing us to complete everything on time and better the business.”
~Ryan Duce, Electrical Engineer
Impact
The entire process, custom built for GDI, was completed on-time and within budget- allowing the receipt of material shipments by truck as scheduled for the first date of operation in the new facility. This ensured uninterrupted production upon transferring from the original manufacturing facility to the new state of the art operation. GDI has already realized the impact of this initiative noting the ability to process twice the level of materials in the same time period as previous production runs. Having the batch process acknowledged in the HMI prior to each step being conducted has ensured the level of quality and consistency the team was seeking.
The entire production process has been transformed, providing controls…
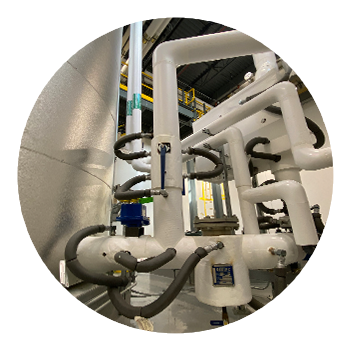