Situation
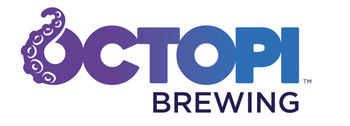
Octopi is the first contract beverage facility in the Midwest. It was built from the ground up to meet the needs of the modern beverage client, featuring a system capable of handling just about any type of beverage – from a classic Czech-style Pilsner to cold-pressed coffee. Octopi’s state-of-the-art packaging lines are one of the most efficient on the market today, capable of filling multiple styles and sizes of bottles and cans – allowing for unprecedented flexibility in packaging their customer’s products.
The company takes its name from the octopus, symbolizing their objective in the world of beverages. The octopus, just like the beverage industry, is transforming and reinventing itself every single day. Based on this, it’s crucial Octopi stays ahead of the game through an innovative approach to leveraging technology, always adjusting for upcoming market trends and customer needs. Sharing a similar philosophy of innovation, optimization and efficiency, Automation Solutions LLC proved to be an ideal manufacturing technology partner.
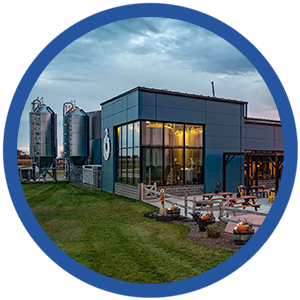
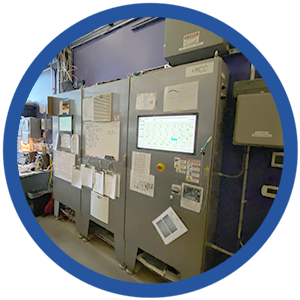
Opportunity
Octopi’s quest to maintain their position as one of the most innovative breweries in the country led them to pursue various automation suppliers. After years of working with vendors lacking the true expertise and shared vision, they contracted our automation team in 2018 to chart a path forward. The project’s objective was to lead the transition from being a “manual” brew house to one filled with cutting edge automation – offering the highest degree of quality controls and efficiency. Any great brewer (or producer of beverages) understands a key obstacle to overcome in the production process is the ability to repeatedly produce and package the same recipe, ensuring a consistent tasting product across multiple batches. Obtaining this consistency becomes more of a challenge when multiple personnel and shifts are introduced, specifically in cases where the recipes are dependent upon the operators’ keying in the proper information. In those instances, the process timing with a manual system is basically at the mercy of the operator. Octopi is now able to showcase their ability to overcome this challenge to both existing and new potential customers, demonstrating that the process control upgrade is an integral factor when clients choose Octopi for producing their product.
Since 2018, additional work has been contracted between Automation Solutions LLC and Octopi, reinforcing their commitment to providing customers with the most optimal solution to produce their products. The length of this on-going relationship also highlights each company’s willingness to work together in building solutions as long-term partners. Octopi’s desire to be the best at what they do directly correlates with Automation Solutions LLC’s philosophy of providing custom-tailored automation solutions offering:

Innovation
Leveraging the latest technology to provide more consistent, repeatable outcomes, while elevating operational throughput via processes designed to future-proof businesses.
Optimization
Pursuing the most effective process and custom-tailored solutions to achieve desired outcomes; and establishing protocols for preventative maintenance to minimize downtime.
Efficiency
Partnering to find cost/time-saving solutions across operations, resulting in higher throughput and decreased machine downtime.
Octopi’s ability to react to market needs, combined with the on-time and in-budget solutions introduced by Automation Solutions LLC, have directly correlated with fueling tremendous brewery growth, resulting in the need for expansion. Two additional brew houses have since been completed, along with the addition of new equipment requiring seamless infusion with the existing production process. Once again, a custom solution proved to be the best path to success as opposed to retrofitting “off the shelf” processes and products. The new system is thoughtfully designed for a specific intent, as opposed to being a modification of something pre-existing that was altered to “hopefully” get the job done. And while that solution may sound cost prohibitive, it actually provided this customer the highest of quality solutions at an affordable investment – immediately contributing to ROI.
Implementation
The complexity of Octopi’s business has them working with various systems and suppliers. In addition to delivering solutions that have been both on-time and in-budget, Isaac Showaki (President of Octopi and Untitled Art Beers) says what’s impressed him most about Automation Solutions LLC has been their ability to partner with the company’s other contractors through the successful coordination and communication of their projects. Historically, suppliers had been working within their own silos – not openly communicating with one another. Automation Solutions LLC helped to overcome those challenges and implement the best solution possible.
Octopi’s former “manual” brew house system was sourced from equipment manufacturer ESAU & HUEBER GmbH out of Germany. The custom designed automated solution features an add on Allen-Bradley CompactLogix system to replace the original Siemens PLC. The Allen-Bradley system was chosen because of its ability (utilizing a gateway bridge module) to interface with all of the existing Siemens Profibus components. An InduSoft SCADA server was added allowing for multiple client connections to the new brew house controls.
The two additional brew house expansions to the Allen-Bradley and InduSoft system were commissioned in February of 2019. The first expansion was highlighted by the addition of a WORT Receiver vessel, followed by a Sucrose Addition Tank. The automation was added to the ‘wet’ brewing process initiating at the Mash Tun which pumps to the Lauter Tun, then pumping to the WORT Receiver, followed by the Kettle, the Whirlpool (in select instances pumping to the Hop Rocket), and finally pumping through the cooler to the fermenting tanks. The new process allowed for tighter control over the addition of water, steam heating, grain and hops additions, and finally cooling before transferring to the fermenters.
The old process was highly contingent upon the day shift brewer (which allowed for variability based upon how the operator was trained vs. the other shift brewers. The biggest differentiator with this particular automation was associated with the action of the “Deep Cut” and “Under Let” at the Lauter Tun. Each operator has the ability to select “Deep Cut” and “Under Let” at any time; however the new system automatically initiates the process if not selected at the exact time they are needed.
“The octopus possesses qualities that symbolize our objectives in the world of beverages. We are our client’s extra limb, helping them to grow their business. We are a co-packer specializing in high quality beverages made by the most talented team with state-of-the-art equipment. At Octopi, we aspire to produce the best quality beverages while offering unparalleled customer service. Our partnership with Automation Solutions LLC ensures we are able to deliver all of our customers’ goals.”
~Isaac Showaki, President Octopi
Impact
“Automation Solutions LLC’s work allows Octopi to focus on the quality of the beverages manufactured. The solution eliminates any doubt customers have in terms of consistency – showcasing how automation can eliminate variability, guaranteeing an optimal product every time”
~James Hanley, Sr. Controls Engineer
Automation Solutions LLC is one of the few service providers possessing the in-house expertise of integrating Siemens hardware with an Allen-Bradley PLC. Our expertise in this area proved to be a crucial and cost-savings benefit to Octopi. In all, the customization of the system has increased the brewery’s output by over 40%. Automation Solutions LLC’s ability to listen, partner, research and custom craft the most effective solution in this instance helped Octopi to:
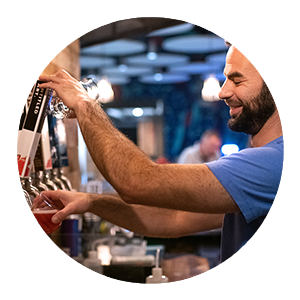