It is important to have a plan when it comes to the maintenance of automated systems.
One item is usually a contingency plan outlining what to do if the system fails, and another item would include preventative measures on how to combat against downtime. Unfortunately, the approach many companies decide to take is reactive instead of proactive. The mindset they have is “if nothing is currently broken, there is nothing to fix”. The consequences of this mindset can be costly. The older a system is, the costlier the reactive approach becomes.
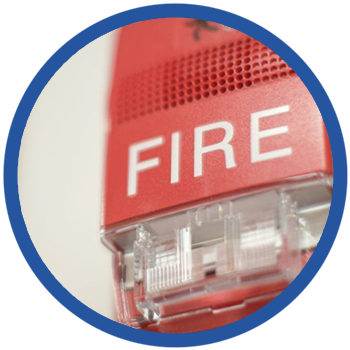
Why is it so important to keep automated systems up-to-date?
Keeping these systems current can be crucial in the event of a device or system failure. Wear is rarely observable in control systems, and is typically only discovered when a device fails. Unfortunately, most automation controls manufacturers have a certain time limit for how long they support products. After that period, the parts are discontinued and are no longer available as new components. This can make finding replacement parts difficult or impossible once they are discontinued, especially if the part has been discontinued for years or decades. If you’re lucky, you might find a part somewhere while searching the vast depths of the internet. Trying to find a part for an obsolete or antiquated control system is much like trying to find a battery for a cellphone from the early 90’s. Cellphones have changed so much in the past 20 years that it would be nearly impossible.
But what if the part can’t be found?
If the part isn’t found a company can be stuck with a down system or device until the system can be upgraded. This is a huge consequence because downtime is costly and can affect productivity. In this case, the company that did not plan ahead is left with a productivity “fire” that needs to be put out. However, if they would have kept the system up-to-date they would have alleviated some pressure. The company would have had the assurance that replacement parts would be available when needed. An often-overlooked consequence of the “panic” upgrade (repair) is that the decisions influenced by urgency don’t consider the potential for process improvements that would be suggested with a proper system analysis.
Are there more advantages?
Keeping automated systems up-to-date is not only beneficial in preventative planning, it can also provide faster communication speeds than its predecessors. If the system is current and up-to-date, a full systems integration can be much simpler and could potentially cost less. Also, most of the technology that is available on automated systems today was unavailable years ago. Current automated systems possess the latest in technology and can communicate at state of the art levels, among many other things.
Having a plan about when to upgrade controls systems isn’t only a smart idea—I would consider it a necessity. They should be kept current to ensure the highest possible levels of productivity, as well as to make sure that parts are available when systems fail. The consequences of not having a plan on when to upgrade can leave you stuck without a readily-available solution.
Let’s Get Connected