What Is DeviceNet & Why Do Companies Use It?
DeviceNet is a communication protocol used in industrial automation systems for connecting and controlling devices like sensors, actuators, and other industrial equipment on a network. It is based on the Controller Area Network (CAN) technology for industrial use due to its robustness and reliability. Here’s why many manufacturers use it:
Efficient Device Communication
DeviceNet allows devices from different manufacturers to communicate seamlessly on the same network. This interoperability simplifies integration and reduces the complexity of wiring in industrial environments. Each device (sensors, motors, etc.) is connected to the same communication bus, reducing the number of physical connections needed.
Reduced Wiring
Traditional systems often require dedicated wiring for each device. With DeviceNet, multiple devices can share the same communication and power bus, which drastically reduces the amount of wiring required. This leads to lower installation costs and easier maintenance.
Real-time Control
DeviceNet offers real-time communication capabilities, allowing systems to monitor and control devices efficiently. Its built-in prioritization of messages ensures that critical data, like emergency stop commands, are delivered immediately.
Simplified Device Management
DeviceNet supports “plug and play” functionality, meaning devices can be easily added or removed from the network without requiring a complete reconfiguration of the system. This makes it easier to expand or modify automation systems.
Diagnostics and Monitoring
DeviceNet provides extensive diagnostic capabilities, enabling manufacturers to monitor the status and health of devices on the network. This proactive maintenance can help reduce downtime and improve system reliability.
Cost Efficiency
By reducing wiring, simplifying installation, and supporting devices from multiple vendors, DeviceNet helps manufacturers save both time and money.
Industry Standard
DeviceNet has become a widely accepted communication standard in industrial automation, supported by many device manufacturers. This broad adoption ensures that companies can source compatible equipment from multiple vendors.
In summary, manufacturers use DeviceNet to streamline industrial automation processes, reduce wiring complexity, enhance real-time control, and improve overall system flexibility and efficiency. However, manufacturers are transitioning to Ethernet-based solutions like EtherNet/IP due to its higher bandwidth, faster communication speeds, and ability to integrate with enterprise-level systems. EtherNet/IP is also part of the Common Industrial Protocol (CIP), the same protocol family as DeviceNet.
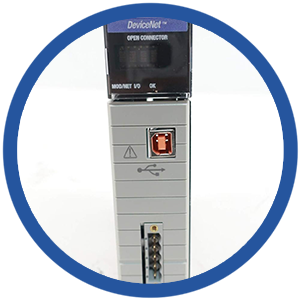
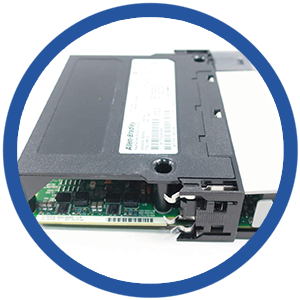
How To Determine if
You Have DeviceNet
While it’s always best to work with experts at a preferred integrator, there are ways to potentially determine if you have DeviceNet installed in your system.
Look for DeviceNet Cables and Connectors
DeviceNet cables are typically thick and have a distinct look. They are made to carry both data and power and often come in a shielded cable design to reduce electromagnetic interference.
Connectors: The standard DeviceNet connector is a 5-pin round connector, which is used to connect devices to the DeviceNet network. The pins are for power (+V, -V), ground, and two communication lines (CAN_H, CAN_L).
Check the Network Layout
DeviceNet operates as a bus network, where multiple devices (such as sensors, actuators, and controllers) are connected to a single communication line. If you see several devices connected to the same line with T-connectors or drop lines, this is a potential indicator of DeviceNet.
Identify DeviceNet-Specific Hardware
DeviceNet Scanners or Modules: Look for DeviceNet communication modules in your system, such as Allen-Bradley’s 1756-DNB or 1747-SDN. These modules are used to interface the network with controllers like PLCs.
Node Identifiers: Each device on the DeviceNet network is assigned a unique node ID. You may see these IDs labeled on devices, indicating they are part of a DeviceNet network.
Check the System’s Configuration Software
RSNetWorx for DeviceNet is a common configuration software for DeviceNet systems, especially for systems using Rockwell Automation hardware. If you have access to the system’s software, check if RSNetWorx is being used.
Examine Device Labels and Documentation
Devices connected to a DeviceNet network will often be labeled as “DeviceNet” compliant. Look for this marking on sensors, actuators, or any network devices. You can also refer to device manuals or datasheets to confirm if they are DeviceNet-compatible.
Use Diagnostic Tools
You can use diagnostic tools like a DeviceNet analyzer to scan the network. It will detect and display the devices connected to the DeviceNet bus, showing you a list of connected nodes and their status.
PLC Program
If you have access to the PLC program, it might include configurations for a DeviceNet scanner module. Look for DeviceNet-related tags or instructions in the program that manage the data exchanged with DeviceNet devices. By checking the network layout, cables, connectors, hardware, software, and device documentation, you can confirm whether your system is using DeviceNet.
Why Might You Consider
Transitioning Away
From DeviceNet
There are several reasons why you may move away from DeviceNet. While it’s been a reliable and robust protocol in industrial automation, its limitations in terms of speed, scalability, distance, and compatibility with modern systems make it less suitable for today’s manufacturing needs. Moving to newer, Ethernet-based protocols can offer improved performance, better integration, enhanced diagnostics, and long-term support, ultimately leading to more efficient and future-ready automation systems. And with limited support, now could be the right time to upgrade.
Limited Bandwidth and Data Transfer Speeds
DeviceNet is based on the CAN (Controller Area Network) protocol, which may be insufficient for modern applications that require higher data transfer speeds, especially for systems involving large volumes of data or real-time control.
Scalability Challenges
DeviceNet networks are typically limited in the number of devices they can handle. A standard DeviceNet network can only support a maximum of 64 nodes, which can be restrictive in larger, more complex systems. Ethernet-based solutions like EtherNet/IP can scale much more easily.
Limited Distance
The maximum length of a DeviceNet network cable is relatively short (100-500 meters depending on the data rate), which limits the physical reach of the network. Ethernet-based networks allow for longer cable runs (up to 100 meters per segment without repeaters).
Outdated Technology
Newer protocols such as EtherNet/IP, PROFINET, or Modbus TCP provide enhanced diagnostics, better integration with IT systems, and support for more advanced industrial applications, such as Industrial Internet of Things (IIoT) and Industry 4.0.
Maintenance and Troubleshooting Difficulties
DeviceNet troubleshooting can be time-consuming and difficult, as diagnostic capabilities are more limited compared to Ethernet-based protocols. DeviceNet issues such as network noise or failed devices may require significant effort to diagnose.
Incompatibility with Modern Systems
DeviceNet may not integrate easily with modern automation systems that rely on Ethernet-based communication. This includes compatibility with higher-level systems like SCADA, MES, or enterprise IT systems, which are typically built on Ethernet standards.
Decreasing Vendor Support
While Rockwell still supports DeviceNet, their focus has shifted toward EtherNet/IP and other modern communication standards. As a result, manufacturers may find fewer updates, fewer new products, and reduced support for DeviceNet over time. As DeviceNet becomes less common, sourcing replacement parts and finding technicians who are familiar with it may become more challenging, potentially leading to longer downtimes.
Cost of Ownership
Maintaining older DeviceNet systems may become increasingly expensive due to the higher cost of spare parts, the need for specialized knowledge, and limited diagnostic capabilities.
Enhanced Security Features
DeviceNet lacks many modern cybersecurity features, as it was not designed with the same security considerations required in today’s networked industrial environments.
Future-Proofing
As industrial automation advances, manufacturers are adopting technologies like IIoT, machine learning, and edge computing to enhance production efficiency and predictive maintenance.
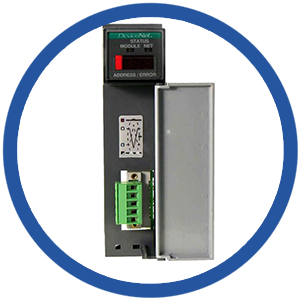
Let’s Get Connected