With the new year here, many companies will be looking to budget needed updates to their systems. A company that manufactures goods should always be keeping an eye on the age of their control system as well as how it is operating. Is it efficient? Does it have unexpected errors or cause a loss in productivity? Sometimes it can be hard to know the right time to budget an upgrade to your control system. The following seven reasons, while not necessarily true in all cases, are good indicators that your system is aging and should be given attention before major errors occur.
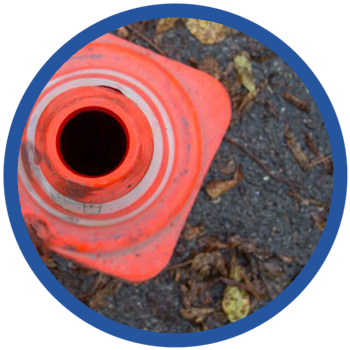
Warning signs that you may need a new control system:
1. Discontinued technical support
A good indicator that your control system may be old and on its way out the door is that it’s hard to find someone to provide technical support. There are a wide variety of technicians with different knowledge and skills pertaining to different vendors and systems. But if you find it almost impossible to find someone to service your system, take that as an indicator that your system is or is well on its way to being antiquated.
2. Difficulty finding spare parts
If you notice that finding spare parts becomes more difficult over time, then you may have a system that needs updating. Control System manufacturers only produce parts for so long before they discontinue items. There may be a stock of spare parts available in a warehouse, but after the item is discontinued and the supply is gone there will be no guarantee that you’ll find the part you need to repair your system.
3. Difficult to provide internal and third-party support
This sort of goes hand in hand with having issues finding a technician to service your system. If you are finding that it is hard to find someone in-house or even from a third-party to provide support on your system, there is a good chance it could be aging. Employees or even third parties are rarely given detailed technical training on systems that are almost irrelevant. So, if your go-to support person retires and you can’t find someone else internally or from a third-party to replace him/her then it may be time for an upgrade.
4. Reliability issues
No one wants an unpredictable control system. If your system goes down frequently or requires constant repair, then you may need to make a change. Unfortunately, your system won’t just get better on its own one day and cease to have issues. Upgrading to a new system kills the reliability issue and keeps your company from suffering unpredictable production time losses.
5. Better plant performance needed
Maybe your system is working great (good for you!) but you need better performance. It’s possible that your system is simply too slow, or maybe your production demands have changed and your current system is simply not capable of producing the results you need. Obviously, if your current system can’t meet your expectations it is time to make a change. Upgrading to a new system with cutting-edge technology ensures quicker production times and increased capabilities.
6. Can’t connect with new or existing third-party applications
Third party applications are applications created from a company other than the one that created the control system. These applications are updated from time to time, and the updates are not always compatible with existing control architecture. Firmware changes and hardware changes create version mismatches. If an update is made to the third-party application, but not the control system, then the application may no longer be compatible. The same goes for connecting a new third-party application to an older control system—they simply may not be compatible because of software and hardware mismatches. If a certain third-party application is essential to your business function and your control system no longer supports it, then there is a need to update your control system.
7. Major plant expansion that can’t be accommodated by the existing control system
If your plant is planning a major expansion it could be difficult to piece together different components from the old and new controls systems. When new equipment is part of the expansion, there is a probability that communication errors will occur with older control systems. This means that the old and new components may not communicate properly or may not communicate at all. This is similar to #6 in that the technology of older systems is likely not compatible with new components.
Whether your company has one or all of the warning signs is important to consider the cost of not keeping your systems current. It is always better to be proactive instead of fighting issues as they arise.
Let’s Get Connected